Väsimusmurru jälgimiseks ja murdumismehhanismi analüüsimiseks kasutati skaneerivat elektronmikroskoopi; samal ajal viidi dekarbureeritud katsekehadele läbi erinevatel temperatuuridel tsentrifuugimise painutamise väsimuskatse, et võrrelda testitava terase väsimisiga koos dekarburiseerimisega ja ilma ning analüüsida dekarburiseerimise mõju katseterase väsimusvõimele. Tulemused näitavad, et kuna kuumutamisprotsessis toimub samaaegne oksüdatsioon ja dekarburisatsioon, näitab nende kahe vastastikmõju, mille tulemuseks on täielikult dekarbureeritud kihi paksus koos temperatuuri kasvuga, suurenemise ja seejärel vähenemise trendi. täielikult dekarbureeritud kihi paksus saavutab maksimaalse väärtuse 120 μm temperatuuril 750 ℃ ja täielikult dekarbureeritud kihi paksus saavutab minimaalse väärtuse 20 μm temperatuuril 850 ℃ ning katseterase väsimuspiir on umbes 760 MPa ja katseterase väsimuspragude allikaks on peamiselt Al2O3 mittemetallilised kanded; dekarburiseerimiskäitumine vähendab oluliselt katseterase väsimuse kestust, mõjutades katseterase väsimust, mida paksem on dekarburiseerimiskiht, seda madalam on väsimuse kestus. Selleks, et vähendada karburiseerimiskihi mõju katseterase väsimusvõimele, tuleks katseterase optimaalseks kuumtöötlustemperatuuriks seada 850 ℃.
Käigukast on auto oluline komponentSuurel kiirusel töötamise tõttu peab hammasratta pinna haarduval osal olema kõrge tugevus ja kulumiskindlus ning hambajuurel peab olema pideva korduva koormuse tõttu hea paindeväsimusvõime, et vältida materjalini viivate pragude tekkimist. luumurd. Uuringud näitavad, et dekarburiseerimine on oluline tegur, mis mõjutab metallmaterjalide tsentrifuugimise painde väsimust, ja tsentrifuugimise painde väsimus on toote kvaliteedi oluline näitaja, mistõttu on vaja uurida katsematerjali dekarburiseerimise käitumist ja tsentrifuugimise painde väsimust.
Selles artiklis kuumtöötlemisahju 20CrMnTi hammasratta terasest pinna dekarburiseerimise katse, analüüsida erinevaid kuumutustemperatuure katse terasest decarburization kihi sügavus muutuva seaduse; kasutades QBWP-6000J lihtsa tala väsimuse testimismasinat testitava terase pöörleva painde väsimuse katsel, testitava terase väsimustõhususe määramiseks ja samal ajal analüüsimaks dekarburiseerimise mõju katseterase väsimustõhususele tegeliku tootmise parandamiseks. tootmisprotsessi, tõsta toodete kvaliteeti ja pakkuda mõistlikku viidet. Katseterase väsimusjõudlus määratakse tsentrifuugimise painutamise väsimuse katsemasinaga.
1. Katsematerjalid ja -meetodid
Katsematerjal 20CrMnTi hammasrataste terasest seadme jaoks, mille peamine keemiline koostis on näidatud tabelis 1. Dekarburiseerimiskatse: katsematerjal töödeldakse Ø8 mm × 12 mm silindriliseks prooviks, pind peaks olema hele ilma plekkideta. Kuumtöötlusahi kuumutati temperatuurini 675 ℃, 700 ℃, 725 ℃, 750 ℃, 800 ℃, 850 ℃, 900 ℃, 950 ℃, 1000 ℃ ja seejärel õhutati ruumi 1 h. Pärast proovi kuumtöötlemist häälestamise, lihvimise ja poleerimisega 4% lämmastikhappe alkoholilahuse erosiooniga, metallurgilise mikroskoopia kasutamine, et jälgida terasest dekarburiseerimiskihti, mõõtes dekarbureerimiskihi sügavust erinevatel temperatuuridel. Spin-painutus väsimuskatse: katsematerjal vastavalt kahe tsentrifuugimise painutamise väsimusproovide rühma töötlemise nõuetele, esimene rühm ei tee karburiseerimiskatset, teine rühm dekarburiseerimiskatset erinevatel temperatuuridel. Kasutades tsentrifuugimise painutamise väsimuse testimismasinat, testitakse kahte katseterase rühma tsentrifuugimise painutamise väsimuse testimiseks, kahe katseterase rühma väsimuspiiri määramist, kahe katseterase rühma väsimuse kestuse võrdlemist, skaneerimise kasutamist. elektronmikroskoobi väsimusmurdude vaatlus, proovikeha murdumise põhjuste analüüsimine, et uurida katseterase väsimusomaduste dekarburiseerimise mõju.
Tabel 1 Katseterase keemiline koostis (massiosa) massiprotsent
Küttetemperatuuri mõju dekarburiseerimisele
Dekarburiseerimise korralduse morfoloogia erinevatel kuumutamistemperatuuridel on näidatud joonisel 1. Nagu jooniselt näha, siis kui temperatuur on 675 ℃, ei paista proovi pinnal dekarburiseerimiskihti; kui temperatuur tõuseb 700 ℃-ni, hakkas õhukese ferriidi dekarburiseerimiskihi jaoks tekkima proovipinna dekarburiseerimiskiht; kui temperatuur tõuseb 725 ℃-ni, suurenes proovipinna dekarburiseerimiskihi paksus märkimisväärselt; 750 ℃ dekarburiseerimiskihi paksus saavutab maksimaalse väärtuse, sel ajal on ferriidi tera selgem, jämedam; kui temperatuur tõuseb 800 ℃-ni, hakkas dekarburiseerimiskihi paksus oluliselt vähenema, selle paksus langes pooleni 750 ℃; kui temperatuur jätkab tõusmist 850 ℃-ni ja dekarburiseerimise paksus on näidatud joonisel 1. 800 ℃, hakkas kogu dekarburiseerimiskihi paksus oluliselt vähenema, selle paksus langes poole võrra 750 ℃-ni; kui temperatuur jätkab tõusmist 850 ℃-ni ja kõrgemale, väheneb katseterase täielik dekarburiseerimiskihi paksus, poole dekarburiseerimiskihi paksus hakkas järk-järgult suurenema, kuni kogu dekarburiseerimiskihi morfoloogia kadus, poole dekarburiseerimiskihi morfoloogia muutus järk-järgult selgeks. On näha, et täielikult dekarbureeritud kihi paksust koos temperatuuri tõusuga suurendati ja seejärel vähendati, selle nähtuse põhjuseks on proovi kuumutusprotsessis samaaegne oksüdatsiooni- ja dekarburiseerimiskäitumine, ainult siis, kui dekarburiseerimise kiirus on kiirem kui oksüdatsiooni kiirus, ilmneb dekarburiseerimise nähtus. Kuumutamise alguses suureneb täielikult dekarbureeritud kihi paksus järk-järgult koos temperatuuri tõusuga, kuni täielikult dekarbureeritud kihi paksus saavutab maksimaalse väärtuse, sel ajal temperatuuri tõstmise jätkamiseks on proovi oksüdatsioonikiirus kiirem kui dekarburiseerimise määr, mis pärsib täielikult dekarbureeritud kihi suurenemist, mille tulemuseks on langustrend. On näha, et vahemikus 675 ~ 950 ℃ on täielikult dekarbureeritud kihi paksuse väärtus temperatuuril 750 ℃ suurim ja täielikult dekarbureeritud kihi paksuse väärtus temperatuuril 850 ℃ on väikseim, seetõttu soovitatakse katseterase kuumutustemperatuuriks olla 850 ℃.
Joonis 1 1 h erinevatel kuumutustemperatuuridel hoitud katseterase dekarbureeritud kihi histomorfoloogia
Võrreldes pooldekarburiseeritud kihiga on täielikult dekarbureeritud kihi paksusel materjali omadustele tõsisem negatiivne mõju, see vähendab oluliselt materjali mehaanilisi omadusi, näiteks vähendab tugevust, kõvadust, kulumiskindlust ja väsimuspiiri. jne ning suurendab ka tundlikkust pragude suhtes, mis mõjutab keevitamise kvaliteeti ja nii edasi. Seetõttu on täielikult dekarbureeritud kihi paksuse reguleerimine toote jõudluse parandamiseks väga oluline. Joonisel 2 on kujutatud täielikult dekarbureeritud kihi paksuse variatsioonikõverat temperatuuriga, mis näitab selgemini täielikult dekarbureeritud kihi paksuse varieerumist. Jooniselt on näha, et täielikult dekarbureeritud kihi paksus on 700 ℃ juures vaid umbes 34 μm; kui temperatuur tõuseb 725 ℃-ni, suureneb täielikult dekarbureeritud kihi paksus oluliselt 86 μm-ni, mis on rohkem kui kaks korda suurem kui täielikult dekarbureeritud kihi paksus temperatuuril 700 ℃; kui temperatuur tõstetakse 750 ℃-ni, siis täielikult dekarbureeritud kihi paksus Kui temperatuur tõuseb 750 ℃-ni, saavutab täielikult dekarbureeritud kihi paksus maksimaalse väärtuse 120 μm; kui temperatuur jätkab tõusmist, hakkab täielikult dekarbureeritud kihi paksus järsult vähenema, 800 ℃ juures 70 μm-ni ja seejärel 850 ℃ juures minimaalse väärtuseni umbes 20 μm.
Joon.2 Täielikult dekarbureeritud kihi paksus erinevatel temperatuuridel
Karburiseerimise mõju väsimusvõimele tsentrifuugimisel
Dekarburiseerimise mõju uurimiseks vedruterase väsimusomadustele viidi läbi kaks tsentrifuug-painutusväsimuskatsete rühma, esimene rühm oli väsimustest otse ilma dekarburiseerimiseta ja teine rühm oli väsimustestid pärast dekarburiseerimist samal pingel. tasemel (810 MPa) ja dekarbureerimisprotsessi hoiti temperatuuril 700–850 ℃ 1 tund. Esimene katsekehade rühm on näidatud tabelis 2, mis näitab vedruterase väsimuse kestust.
Esimese proovikehade rühma väsimuse kestus on näidatud tabelis 2. Nagu tabelist 2 näha, tehti katseterasele ilma dekarburiseerimiseta ainult 107 tsüklit 810 MPa juures ja murdumist ei toimunud; kui pingetase ületas 830 MPa, hakkasid osad isendid murduma; kui pingetase ületas 850 MPa, purunesid kõik väsimusproovid.
Tabel 2 Väsimuse eluiga erinevatel stressitasemetel (ilma dekarburiseerimiseta)
Väsimuspiiri määramiseks kasutatakse katseterase väsimuspiiri määramiseks rühmameetodit ning pärast andmete statistilist analüüsi on katseterase väsimuspiiriks ca 760 MPa; testitava terase väsimusea iseloomustamiseks erinevatel pingetel joonistatakse SN kõver, nagu on näidatud joonisel 3. Nagu on näha jooniselt 3, vastavad erinevad pingetasemed erinevale väsimuseale, kui väsimuse eluiga 7 , mis vastab tsüklite arvule 107 korral, mis tähendab, et näidis on nendes tingimustes läbi oleku, saab vastavat pingeväärtust lähendada kui väsimustugevuse väärtust, st 760 MPa. On näha, et S - N kõver on oluline materjali väsimuse eluea määramiseks, omab olulist võrdlusväärtust.
Joonis 3 Katseterase pöörleva paindeväsimuskatse SN-kõver
Teise katsekehade rühma väsimuse kestus on näidatud tabelis 3. Nagu tabelist 3 näha, väheneb pärast katseterase dekarburiseerimist erinevatel temperatuuridel tsüklite arv ilmselgelt ja neid on rohkem kui 107 ja kõik väsimusproovid on murdunud ja väsimuse kestus on oluliselt vähenenud. Koos ülaltoodud dekarbureeritud kihi paksusega koos temperatuurimuutuse kõveraga on näha 750 ℃ dekarbureeritud kihi paksus suurim, mis vastab väsimuse kestuse madalaimale väärtusele. 850 ℃ dekarbureeritud kihi paksus on väikseim, mis vastab väsimuse eluea väärtusele on suhteliselt kõrge. On näha, et dekarburiseerimiskäitumine vähendab oluliselt materjali väsimust ja mida paksem on dekarbureeritud kiht, seda madalam on väsimuse eluiga.
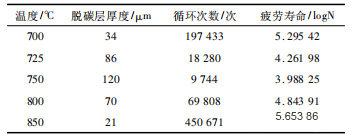
Tabel 3 Väsimuse eluiga erinevatel dekarbureerimistemperatuuridel (560 MPa)
Proovi väsimusmurru morfoloogiat vaadeldi skaneeriva elektronmikroskoobiga, nagu on näidatud joonisel 4. Joonisel 4(a) on pragu allika ala, joonisel on näha ilmselge väsimuskaar, vastavalt väsimuskaarele allika leidmiseks. väsimusest võib näha pragude allikat "kalasilma" mittemetalliliste lisandite jaoks, kergesti tekitatava stressi kontsentratsiooni kandmisel, mille tulemuseks on väsimuspraod; Joonis fig 4(b) pragude laiendusala morfoloogia kohta, on näha ilmseid väsimustriipe, oli jõesarnane jaotus, kuulub kvaasidissotsiatiivsesse murdumisse, kusjuures praod laienevad, mis lõpuks viib murdumiseni. Joonisel 4(b) on kujutatud pragude laienemisala morfoloogiat, on näha ilmseid väsimustriipe jõelaadse jaotuse kujul, mis kuulub kvaasidissotsiatiivsesse murdumisse, ja pragude pideva laienemisega, mis viib lõpuks murdumiseni. .
Väsimusmurdude analüüs
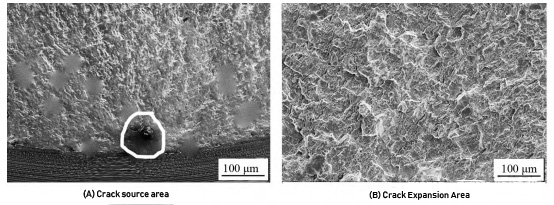
Joonis 4 Katseterase väsimusmurdepinna SEM-morfoloogia
Joonisel fig 4 kujutatud lisandite tüübi määramiseks viidi läbi energiaspektri koostise analüüs, mille tulemused on näidatud joonisel 5. On näha, et mittemetallilised kandmised on peamiselt Al2O3 kandmised, mis näitab, et need lisandid on sisendite lõhenemisest põhjustatud pragude peamine allikas.
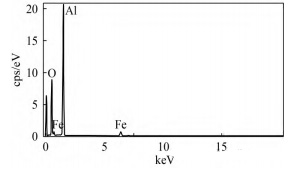
Joonis 5 Mittemetalliliste lisandite energiaspektroskoopia
Järelda
(1) Kuumutustemperatuuri seadmine 850 ℃ minimeerib dekarbureeritud kihi paksust, et vähendada mõju väsimusvõimele.
(2) Katseterase tsentrifuugimise väsimuspiir on 760 MPa.
(3) Katseterase pragunemine mittemetallilistes lisandites, peamiselt Al2O3 segus.
(4) dekarburiseerimine vähendab tõsiselt katseterase väsimuseaega, mida paksem on dekarburiseerimiskiht, seda madalam on väsimuse kestus.
Postitusaeg: 21. juuni 2024